1. Process overview
Film blowing, or blown film extrusion, is a method of producing thin plastic films by melting plastic pellets (such as polyethylene) and then extruding, inflating, and cooling them. In the production of poly mailers, the film blowing process is capable of creating polyethylene films that are waterproof, tear-resistant, and flexible. These characteristics make the films widely applicable in e-commerce, logistics packaging, and other fields. The film blowing process offers high production efficiency and excellent material adaptability, enabling the production of films with varying thicknesses, strengths, puncture resistance, and other properties to meet different demands.
2. Materials
2.1 Common materials
In the production of poly mailers, the most commonly used materials are Low-Density Polyethylene (LDPE) and High-Density Polyethylene (HDPE). These two materials have different physical properties and are suitable for various applications:
-LDPE: Offers high flexibility and ductility, making it ideal for producing films of moderate thickness. Its loose structure gives it excellent stretchability and transparency, commonly used in packaging bags that require flexibility and tear resistance.
-HDPE: Has a higher density and strength, making it more suitable for packaging films that require higher durability, puncture resistance, and tear strength. HDPE films are harder and are used for sturdier packaging needs, such as heavy-item packaging.
LDPE and HDPE can be blended in various proportions to achieve an optimal balance of performance. In addition to the basic physical properties, modern film blowing processes can incorporate features such as anti-static properties, UV resistance, and biodegradability to meet market and user requirements.
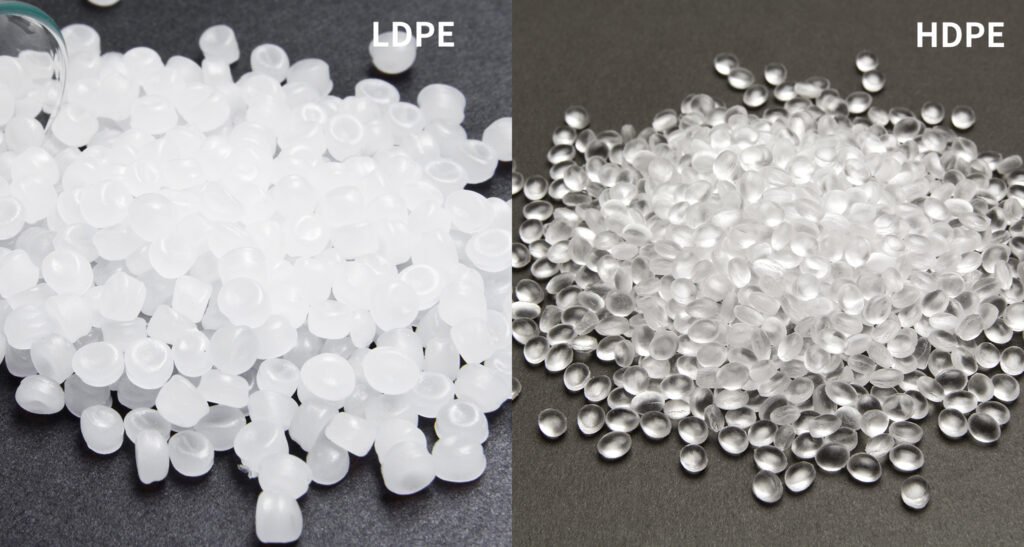
2.2 Special plastic raw materials
Biodegradable plastics: With increasing environmental awareness, the use of biodegradable plastics in film blowing has become more widespread. Biodegradable plastics are primarily categorized into two types: bio-based biodegradable plastics and petroleum-based biodegradable plastics. Examples include polylactic acid (PLA) and polyhydroxyalkanoates (PHA), which are types of biodegradable plastics. These materials are processed in film-blowing machines using specific techniques to create biodegradable plastic films that meet environmental standards.
2.3 Auxiliary materials
In addition to the primary plastic raw materials, auxiliary materials such as plasticizers, stabilizers, and pigments may also be used in the film blowing process. These materials help adjust the properties and appearance of the plastic to better suit the production process and market needs.
3. Equipment
3.1 Components of a film blowing machine
Extruder: The core part of the film blowing machine, responsible for heating, melting, and extruding the plastic pellets. It includes a feeding system that transports the plastic pellets to the hopper of the extruder. The screw is the key component that pushes the plastic pellets forward and melts them through rotation and heat. The heating zone, transition zone, and cooling zone control the temperature to ensure the plastic has the proper flow characteristics for extrusion.
Die head (Die): The part where the extruder connects to the cooling system. It evenly extrudes the melted plastic into a film of a specific width and thickness. The die head typically consists of a mandrel, nip rollers, and an orifice. The mandrel adjusts the film’s width, the nip rollers control the thickness, and the orifice is responsible for extruding the film.
Cooling system: Located between the die head and the winding device, the cooling system cools and solidifies the film to ensure its quality. It usually includes cooling rollers, fans, and air ducts, which rapidly cool the film through water cooling and airflow.
Winding system: The final component of the film blowing machine, responsible for winding the finished film for further processing or use. It typically consists of winding shafts, a tension control system, and a feeding mechanism to roll up the film, controlling the tension during the process.
Other auxiliary equipment: The film blowing machine may also include compressors, blowers, and air rings. Compressors are used to inflate the tube of plastic to form the film, while blowers and air rings help cool the formed film.
Electrical control system: Most film blowing machines are equipped with an operation control cabinet, which uses the electrical control system to operate the entire equipment. This includes main power, motor switches, and temperature controls.
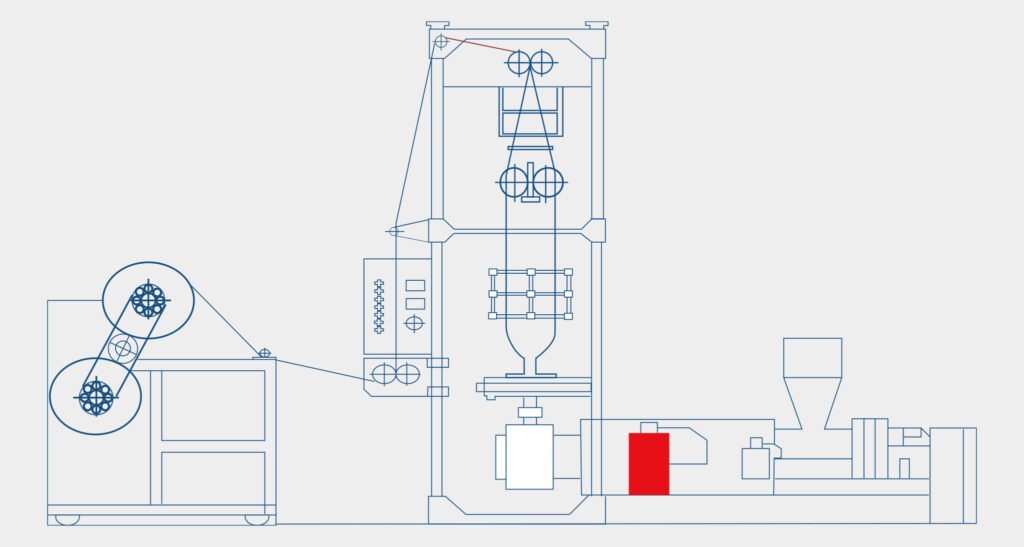
3.2 Types of film blowing machines
Film blowing machines are categorized by the number of die heads:
2-head machine: This machine has two die heads and can extrude two layers or two sets of independent plastic films simultaneously. It is suitable for producing films with different specifications or materials at the same time.
3-head machine: With three die heads, this machine increases production efficiency and can extrude multiple layers of plastic film, allowing the creation of composite films with different materials or colors.
5-head machine: This machine has five die heads and offers greater production capacity and flexibility, suitable for large-scale production or the need to create complex film structures.
8-head machine: With eight die heads, this machine offers high production capacity, suitable for large-scale and highly efficient film production lines. Newer models may include 11 or 12 heads.

3.3 Working principle of film blowing machines
The working principle of the film blowing process involves the following key steps: melting, extrusion, inflation, and cooling:
Melting: Plastic pellets are fed into the hopper of the extruder, where they are heated and melted as the screw pushes them forward. The temperature and time required for melting depend on the type of plastic and the desired properties of the film.
Extrusion: Once the plastic is melted, it is pushed through the die to form a tube of film. The die’s shape determines the cross-section of the film, which is typically cylindrical for film blowing.
Inflation: The tube of molten plastic is inflated with high-pressure air through an air ring, expanding it in the vertical direction to form a bubble-like structure. The inflation level and film thickness are controlled by factors such as air pressure, airspeed, and die diameter.
Cooling: After inflation, the film needs to be cooled and solidified. This is done using either air or water cooling. During cooling, the molecular structure of the film rearranges and solidifies.
Tension and Winding: After cooling, the film is pulled through tension rollers and wound into rolls by the winding system.
Subsequent Processing: After winding, the film can be cut, printed, or laminated, depending on the specific needs of different industries.
3.4 Temperature control in film blowing machines
Temperature control is critical to the quality of the film. The temperature of the extruder should be set according to the resin’s melting point. For example, polyethylene (PE) has a melting temperature typically between 105°C and 135°C. Proper temperature settings ensure the uniform plasticization of the resin, which in turn improves the film’s clarity, barrier properties, and durability.
The temperature control system ensures the machine operates within optimal temperature ranges, reducing defects like rough film surfaces or resin decomposition, which can produce undesirable odors.
3.5 Controlling tension and adjusting size and thickness
To ensure uniform tension across both the transverse and longitudinal directions, the film blowing process must carefully control the blow-up ratio (BUR) and draw-down ratio (DDR). The ratio between BUR and DDR directly affects the film’s strength and stability.
BUR (Blow-up Ratio): The BUR controls the stability of the film bubble. An excessively high BUR can lead to instability, causing uneven tension across the film.
DDR (Draw-Down Ratio): DDR adjusts the film’s thickness and controls the quality of the film by manipulating the gap between the die and the take-up rollers.

3.6 Maintenance and inspection of film blowing machines
Regular maintenance and inspection are vital for the efficient operation of film blowing machines. Common checks include the temperature control system, traction speed, heating system, and winding mechanisms. Proper maintenance can prolong the life of the equipment and improve production efficiency.
Temperature control system: Ensure that the temperature settings are correct before starting the machine.
Traction speed: Adjust the traction speed based on the film’s thickness to ensure uniformity.
Winding mechanism: Modern film blowing machines often feature automatic winding systems, which are more efficient and reduce waste.
3.7 Common Issues and Solutions
Film blowing machines may encounter common problems that affect the quality of the film:
Poor transparency: Caused by inadequate resin melting or poor cooling. Solutions include increasing extrusion temperatures and improving cooling efficiency.
Uneven thickness: Caused by uneven die gaps or inconsistent cooling airflow. Solution: Adjust die gap and cooling system.
Bubble instability: This can be caused by incorrect extrusion temperatures or external airflow interference. Solutions include adjusting temperatures and avoiding strong wind during production.
Sticky films with poor opening ability: Caused by incompatible resin or excessive blow-up ratios. Solution: Replace resin, adjust temperatures, or reduce BUR.
Wrinkled films: Caused by uneven thickness or poor cooling. Solutions: Adjust thickness, improve cooling airflow, and adjust tension settings.
Odor in film: Caused by degraded resin or excessive temperatures. Solution: Replace resin and adjust extrusion temperatures.
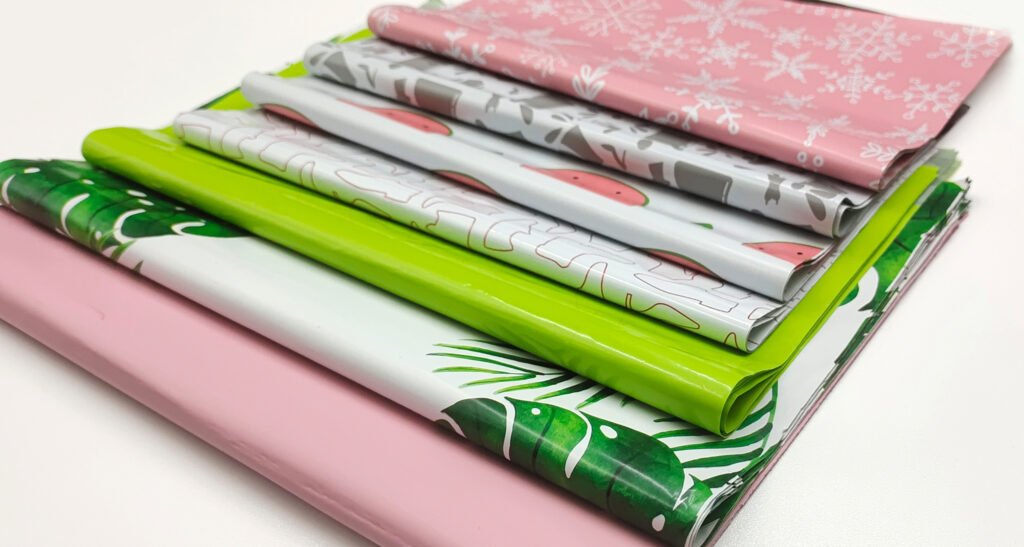
4. Film blowing process
Raw material preparation
The raw material plastic pellets are screened and impurities are removed to ensure the quality of the pellets.
Raw material mixing
In the film blowing process, it is sometimes necessary to mix different colors or types of plastic pellets. This is done by placing the various pellets into a mixer to blend them together.
Feeding
The mixed plastic pellets are fed into the feed section of the extruder. The movement of the screw in the extruder transports the raw materials to the heating section.
Heating
In the heating section, the raw materials are heated to their melting temperature using electric heaters. This heating step must begin in advance and cannot be started once the materials are loaded. Different plastic materials require different heating temperatures and times to ensure the materials are completely melted.
Extrusion
The raw materials enter the extrusion screw of the extruder. Under high temperature and pressure, the melted plastic is forced out. The die controls the outer diameter size of the extruder, while the extrusion volume controls the thickness of the film being extruded.
Cooling and solidification
Once extruded, the film immediately enters a cooling roller. Through the high-speed rotation of the rollers and the cooling water on the surface of the rollers, the temperature of the film is rapidly reduced and solidified.
Stretching
The cooled film enters the stretching rollers. The difference in speed between the rollers causes the film to stretch. During the stretching process, the film’s width and thickness can be adjusted, and its stretching performance is enhanced.
Winding
The stretched film is cut to the required length by a cutting knife. A winding machine then rolls the film into a roll. The tension control of the winding machine is very important, as it ensures the film is tightly wound to prevent loose or deformed rolls.
Inspection
After the film blowing process is complete, the final film is inspected. Common inspection items include film thickness, width, tensile strength, and transparency.
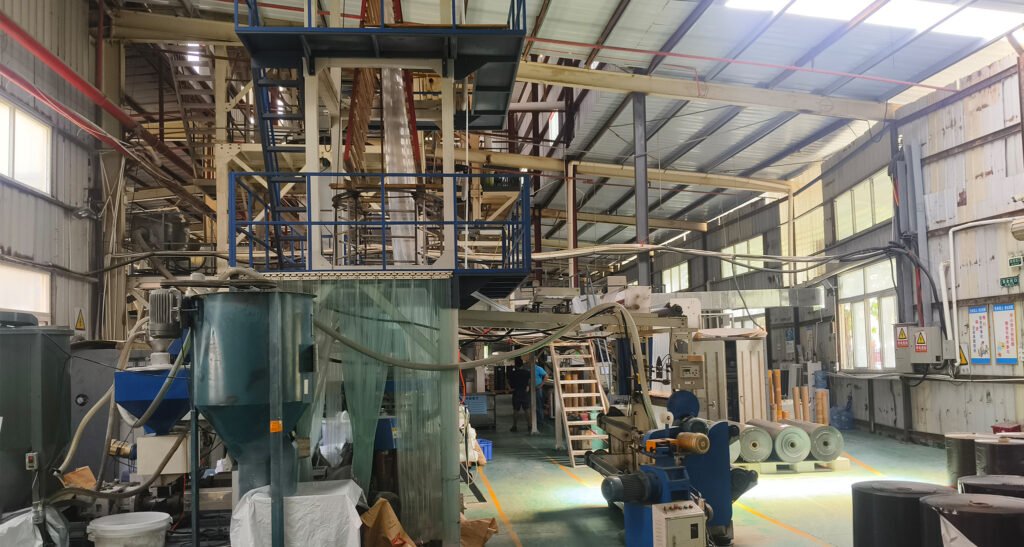
5. Quality control and testing
To ensure the quality of poly mailers, the film blowing process must strictly control various technical parameters to meet the required quality standards. Common quality control tests include:
Thickness uniformity test: The uniformity of the film’s thickness directly affects its tear resistance and puncture resistance. Parameters such as die temperature, air ring cooling, and traction speed control need to be monitored rigorously during the film blowing process.
Tensile strength test: The longitudinal and transverse tensile strength of the film is a key indicator of its durability. Tensile testing ensures the film can withstand the pressures during transportation and use.
Puncture and tear resistance tests: poly mailers need to have good puncture and tear resistance to effectively protect items during transport.
6. Advantages of the film blowing process
Simple equipment, low investment: The equipment required for the film blowing process is relatively simple, making initial investment costs lower. This simplicity also makes machine maintenance and management easier.
Quick results: The production cycle for the film blowing process is relatively short, with quick conversion from raw materials to finished products, allowing for fast market response.
High mechanical properties: blown films have good physical and mechanical properties, such as stretchability and toughness, making them suitable for various applications.
No edge waste, minimal scrap: In the film blowing process, plastic pellets are directly transformed into film, generating minimal edge waste or scrap. Any excess edge material is sucked into the machine for regrinding and remelting, improving raw material utilization.
Adjustable product width: The film blowing process allows for the production of wide films, with flexible control of the film width by adjusting equipment parameters to meet different needs.
Product variety: The film blowing process is suitable for various plastic materials, such as Low-density polyethylene (LDPE) and polypropylene (PP), and can produce a wide range of films with different properties.
Multi-layer co-extrusion capabilities: The film blowing process can achieve multi-layer co-extrusion, allowing for the simultaneous extrusion and blowing of different materials to create films with tailored properties to meet special application needs.
Stable film quality: Due to the stable production process, films made using film blowing technology tend to have consistent quality, ensuring product quality and reducing defect rates.
Energy-efficient and environmentally friendly: The film blowing process can use energy-saving technologies and environmentally friendly materials to reduce energy consumption and pollution emissions, aligning with sustainable development goals.
Wide range of applications: blown films are widely used in packaging and coverage applications in industries such as food, pharmaceuticals, consumer goods, agricultural products, as well as waterproofing and thermal insulation in construction.
7. Energy efficiency and environmental considerations in the film blowing process
As environmental regulations tighten and energy costs rise, energy efficiency and environmental sustainability have become key focuses in the film blowing industry. The latest generation of film blowing equipment uses efficient heating and transmission technologies to significantly reduce energy consumption. Additionally, more and more film blowing processes now use recyclable or biodegradable polyethylene materials to reduce environmental impact.
Energy efficiency: By using variable frequency drives to adjust motor power, energy consumption can be effectively reduced. In addition, efficient heating systems maximize energy use, increasing heating efficiency and minimizing waste.
Environmental protection: Recycling and reusing low-density polyethylene (LDPE) and high-density polyethylene (HDPE) materials can significantly reduce plastic waste. Some companies have also started using biodegradable materials, promoting the transition of plastic packaging to more sustainable practices.
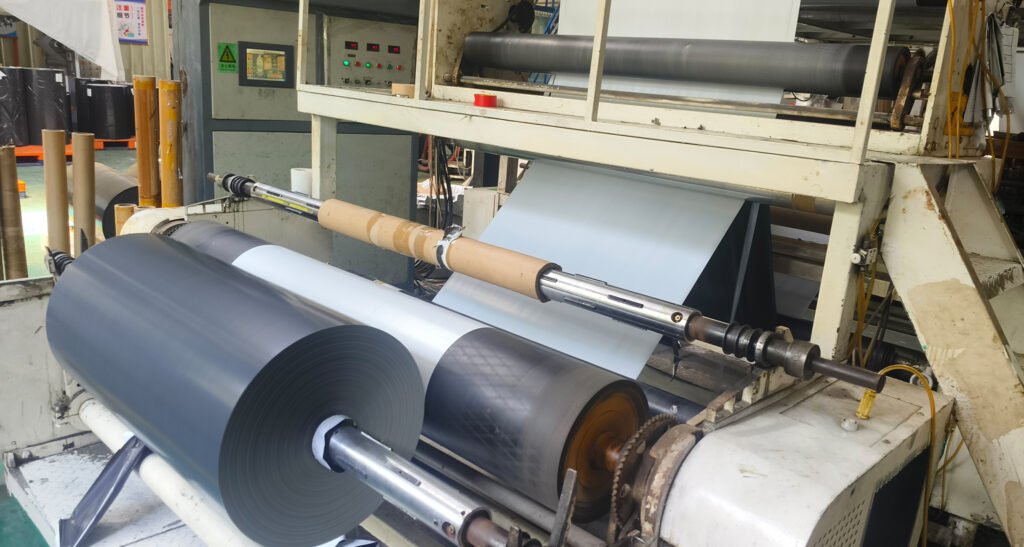
8. Continuous innovation and technological advancements
As the demand for packaging materials in the e-commerce and logistics industries continues to grow, the film blowing process for poly mailers is also undergoing constant development and innovation. Recent technological advancements include:
Multi-layer extrusion technology: The design of multi-layer structures enhances the durability of films and improves their water resistance, moisture protection, and UV resistance.
Use of eco-friendly materials: In line with sustainability trends, more manufacturers are using biodegradable polyethylene and bio-based plastics to drive the green development of the packaging industry.
Development of functional films: Research is underway to develop functional films with properties like UV resistance, anti-static, and antibacterial features, to meet the diverse needs of different markets and customers.
Conclusion
With continuous technological advancements, Package N’ Go’s film blowing process remains at the forefront of sustainable development and intelligent production, offering the packaging industry more environmentally friendly, efficient, and innovative solutions. If you need customized packaging solutions, contact us today! Let us provide your brand with exclusive, eco-friendly packaging support!